- Slipperiness / Lubricity
What is the solid film lubrication coating? Explanation is also provided for Drilube, which provides solid film lubrication coating.
Nevertheless, in the first place, some of you may not know in detail what a solid film lubrication coating is. So, in this article, we will provide an overview of the coating and an introduction to the lubricating substances used. We will also introduce the features and application examples of our Drilube as a solid film lubrication coating; please be sure to read to the end.
What is the solid film lubrication coating?
As a method to improve the sliding performance of parts, the hydrodynamic fluid lubrication of oil or grease is generally used; however, there are cases in which the hydrodynamic lubrication is not applicable for various reasons in the drive transmission components of the equipment. The solid film lubrication coating can be applied to such components that cannot be handled sufficiently by such hydrodynamic lubrication.
The coating is a processing technology that coats the surface of parts with an agent material, which is a mixture of resin and lubricating substances called the solid film lubricant, such as molybdenum disulfide or fluororesin, to form a film and provide lubricity. As a lubricant film, an amorphous hard carbon film with physical properties intermediate between diamond and graphite, called DLC (diamond-like carbon) treatment, or a plating containing solid lubricating pigments, called lubricating plating, may also be used in a similar manner.
Applying a solid film lubrication coating reduces friction because it improves lubricity during sliding. Reduced friction will reduce wear and malfunction of components, resulting in the prolonged service life of components and equipment.
Typical lubrication substances used for solid film lubrication coatings.
Solid film lubricant coatings contain the blended lubricating substances to form a lubricating film. Here are the types and features of lubricating substances used as the main ingredients.
Molybdenum disulfide (MoS2)
Molybdenum disulfide is a lubricating substance produced mainly from a natural ore called molybdenite. It is composed of one molybdenum atom and two sulfur atoms and is represented by the chemical symbol MoS2.
The friction coefficient of molybdenum disulfide is said to be about 0.04, which is excellent in low friction. Furthermore, the high withstanding load performance allows the use of product for both low and high load applications.
The secret to the superior lubricity lies in the molecular structure. The molecular structure of molybdenum disulfide has a layered lattice structure, which is characterized by two sulfur atoms sandwiching a molybdenum atom from both sides. Although molybdenum and sulfur are strongly bonded, between the sulfurs, the bonding is weak in nature. In other words, the sulfur layer, which is weakly bonded, is laterally displaced when force is applied, thereby creating lubricity.
Fluorine resin
Fluororesin is a generic name for a substance that contains fluorine atoms and is used as a raw material for plastics. There are many types such as PTFE (polytetrafluoroethylene), FEP (perfluoroethylene propane copolymer), and PFA (perfluoroalkoxyalkane polymers), which differ in features and withstand temperatures.
The coefficient of friction of fluororesin is said to be 0.03 to 0.04, where PTFE has particularly excellent low-friction performance. There are two types of friction coefficients: static friction coefficient (the friction coefficient that occurs when a stationary object is about to move) and dynamic friction coefficient (the friction coefficient that occurs during movement). Although PTFE is said to have lower values for both, the static friction coefficient is said to be smaller than that of other fluororesins.
Types of fluororesin | Static Friction Coefficient |
---|---|
PTFE | About 0.06 |
PFA | About 0.08 |
FEP | About 0.14 |
*These data indicate only some of the examples, and do not guarantee any values.
PIn the case of PTFE, it is composed of carbon atoms (C) and fluorine atoms (F) and is characterized by its chemically symmetrical and straight-chain molecular structure. Fluorine atoms surround a carbon atom without space, and the smooth state with minimal irregularities produces the slipperiness.
Furthermore, although the performances of fluororesins vary slightly depending on the type, they also have other features, such as non-adhesiveness, chemical resistance, corrosion resistance, thermal resistance, and electrical insulation properties, in addition to low friction properties.
Graphite
Graphite is a substance composed of carbon and is an allotrope of diamond and carbon. It is represented by the elemental symbol C.
Graphite, like molybdenum disulfide, has a layered molecular structure and is characterized by the formation of continuous hexagonal ring layers. While the layer has a strong bonding force in the transverse axis, it has a weak bonding force in the longitudinal axis direction, thereby producing lubricity.
Although the friction coefficient is greater than those of molybdenum disulfide or fluororesins, the overall performance is excellent in terms of low friction properties. The excellent thermal stability also allows the use under high temperature environments with a heat resistance temperature of approximately 500°C.
Other
The standard three main ingredients of solid film lubrication coatings are molybdenum disulfide, fluororesin, and graphite, but the following ingredients may also be used in some cases.
- Tungsten Disulfide
- Boron Nitride
- Mica
- Talc
- Calcium Fluoride
- Silicon Dioxide
- Fullerene
- Carbon Nanotubes
- Soft Metals (gold, silver, copper, lead, and tin)
All of those are used as solid lubricants because of their slippery properties.
What is Drilube?
Drilube is a multifunctional film having a variety of functions in a single film, such as chemical resistance, corrosion resistance, and electrical insulation, in addition to lubricating property. The name is derived from DRY SOLID FILM LUBRICANTs.
Molybdenum disulfide, fluororesin, graphite, and other lubricating substances are used as the main ingredients, to which special binders (bonding ingredients) are added. In addition, the products are made with advanced compounding and dispersion technologies to achieve multifunctional coatings.
Drilube can form a film with the following functions:
- Lubrication property
- Wear resistance
- Corrosion resistance
- Chemical resistance
- Initial conformability
- Electrical insulation property e.t.c
Superior sliding performance and stability even in special and harsh environments of a vacuum, corrosive environments, radiation, lubricant restrictions, low temperatures, and high temperatures. Many substrates can be coated, including metals, rubbers, and plastics; and the coating can be applied to a variety of parts, regardless of size or geometry.
Since it is solid lubrication, the durability and service life of components and materials are prolonged while reducing the maintenance load. Because of its multifunctionality, it has a proven track record in a variety of industries, including automobiles, OA equipment, electrical appliances, semiconductors, optical products, industrial equipment, medical instrument, and aerospace equipment.
Drilube film structure
The film structure of Drilube comes in three types: dispersion type, fluororesin bleed melting type, and fluororesin melting type.
The dispersion type is featured by various functional materials dispersed in the binder. Functionality is added by the binder with other materials, including the lubricating pigments that give low-friction properties.
Fluororesin bleed melting type is a dispersion-type film consisting of fluororesin and binder treated at high temperature. The treatment dissolves and bleeds the fluororesin near the surface to form a film.
Fluororesin melting type is primer-treated to improve adhesion to the substrate. After that, the fluororesin is melted at high temperature to form a coating film. In addition, since fluororesin is used as a base, it features superior non-adhesiveness, chemical resistance, and electrical insulation properties.
Difference in Friction Coefficient Before and After Drilube Treatment
Many of you may be wondering how much the friction coefficient will vary after Drilube treatment. Here, the variation in friction coefficients before and after Drilube treatment is shown for every material.
Material | Before Drilube | After Drilube |
---|---|---|
Aluminum | 1.3 | 0.1 |
Silicone rubber | 1.3 | 0.4~0.6 |
SUS304 | 0.7 | 0.2 |
Polycarbonate | 0.5 | 0.2 |
SPCC-SB | 0.4 | 0.2 |
※The friction coefficient for all materials is reduced. The result shows that Drilube is a film excellent in low-friction property.
The friction coefficient for all materials is reduced. The result shows that Drilube is a film excellent in low-friction property.
Drilube use case examples
Drilube is adopted in many industries as a solid film lubrication coating. Please check out the examples of how it is utilized in every industry to find out the specific items for which it is utilized.
Utilization in Automotive Industry
In the case of automobiles, friction and wear can be reduced by applying a lubricant coating to individual components such as engine parts. The main parts for which Drilube treatment is adopted are as follows:
- Gas injector
- Throttle valve
- Throttle shaft
- Return spring
- Reed plate
- Idle speed valve
- Plunger
- ECV housing
- Accelerator
- EGR housing
- Boot
- Wiper blade
- Diaphragm e.t.c
Use case examples in light electrical appliance industries
Drilube is very actively used in the light electric appliance industries as well, such as AV, OA, and telecommunications. The specific parts coated are as follows:
- Hub
- Rollers
- Paper guide
- Stem
- Case
- Disk guide
- Motor housing
- Magazine spring
- Slider cassette
- Guide shaft
- Clutch e.t.c
Use case examples in optical industries
Coatings are also recommended for optical instrument that utilizes the effects and properties of light, such as digital cameras, microscopes, endoscopes, and projectors. Drilube can be utilized for lubrication coating on the following pars for the purpose of lubrication and matting.
- Kikuza
- Aperture blades
- Lens barrel
- Helicoid
- Zoom shaft
- Light-blocking ring e.t.c
Utilization Examples in Other Industries
In addition to the above, Drilube can be used for lubrication coatings in a wide range of industries, including bicycles and infrastructure equipment, such as the water and gas utilities. Specific parts to which the coatings can be applied are as follows:
- Pulley
- Ball valve
- Rotary valve
- Belt with protrusions e.t.c
General coating process flow when Drilube treatment is ordered.
TOYO Drilube has a coating processing division that can perform Drilube treatment. The general coating flow of Drilube treatment is as below:
Personnel familiar with the properties of the various types of coating agents perform this service, and thus, optimal lubrication coating is achieved. In addition, our highly sophisticated coating technology enables us to respond to a wide range of requirements.
Why not consider Drilube treatment?
Solid film lubrication coating gives lubricity to the surfaces of objects by means of solid lubricants instead of oil or grease. The defective operation or deterioration of equipment and other problems are prevented through reduced friction and wear. The coating process is useful for lubricating the components for which oil or grease cannot be used.
Drilube is a multifunctional coating film, which can form a coating film with the various functions of corrosion resistance, chemical resistance, and electrical insulation, in addition to lubricity. Thanks to its multifunctionality, it can accommodate the needs from a wide range of industries.
TOYO Drilube offers Drilube treatment in both Japan and overseas.
The three overseas factories are located in China, Thailand, and Vietnam. Coating can be processed on a variety of sophisticated parts; please feel free to contact us if you wish to apply Drilube treatment.
Popular post
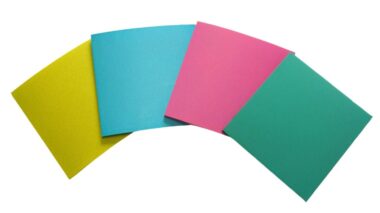
- Slipperiness / Lubricity
-
What is the coating for rubber products (lubricant film for rubber)? The recommended L …
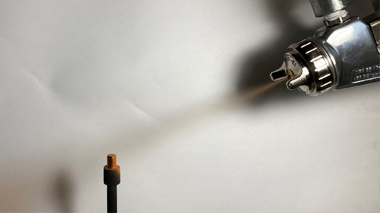
- Slipperiness / Lubricity
-
What is the solid film lubrication coating? Explanation is also provided for Drilube, …
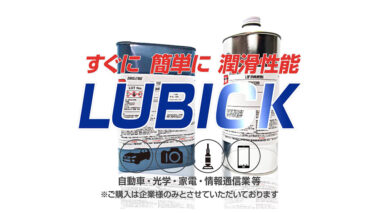
- Slipperiness / Lubricity
-
What is the quick-drying lubricant? LUBICK that can be utilized as a quick-drying lubr …